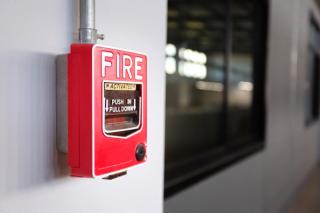
Understanding sound flanking: Fire alarm speaker cable conduits in multi-family buildings
by Neil Vyas
View post
Cement, one of the fundamental materials underpinning our modern world, has maintained a low profile in the eyes of the public for many years, even though it forms a fundamental constituent of the second-most used manmade substance globally: concrete (the first being water). However, CO2 emissions generated by the manufacture of cement are globally significant, estimated as around 7% of global CO2 emissions[1] and after hydrocarbon resource extraction, is a major focus of efforts to reduce CO2 emissions. Reduction of these emissions is fundamental in achieving global net zero CO2 and keeping global warming within 1.5°.
Cement is the glue that binds the ingredients of concrete together to build the buildings and infrastructure we rely on every day. Global cement production in 2020 is estimated at around 4.2Gt and is expected to grow by 12-23% by 2050[2], largely due to population growth, increased urbanisation and installation of low-carbon and renewable energy infrastructure (windfarms, nuclear power stations and solar plants require large amounts of concrete/cement).
Cement is manufactured in the UK and Ireland at a rate of around 15-18Mt per year in a number of locations. Whilst a limited amount of cement is imported and exported overseas and the market is dominated by a small number of global manufacturers, the material is relatively low value and costly to transport: an indigenous supply is important to underpin the construction needs of a country. Extraction of the raw materials and production of cement is a heavily regulated and costly exercise, and the performance of cement is fundamental to the safety and sustainability of the structures it is used to create. Change is costly and more akin to steering a giant cargo ship than a racing yacht.
Change is happening though – CO2 emissions from cement manufactured in the UK have reduced 53% since 1990 to around 0.68 tonnes CO2 per tonne of cement[3]. However, this trend has been flat since 2009.
Tackling the CO2 emissions from cement is complex and multifaceted, and in order to understand the problem a brief science lesson is required.
The most common form of cement used is Ordinary Portland Cement (OPC, or CEM I) which is manufactured by the crushing and burning of limestone, along with shale, clay and other materials to form clinker, then mixing with a variety of other ingredients to achieve the desired properties. Burning of limestone, comprising the mineral calcite (CaCO3), at temperatures in excess of 1400°C creates ‘lime’ (CaO) and releases CO2 in a process known as ‘calcination’. Calcination generates approximately two-thirds of the CO2 emissions (known as process emissions) from cement manufacture. A large proportion of the remainder of emissions comes from generating the heat required for limestone calcination.
The Global Cement and Concrete Association’s (GCCA) Concrete Future – Roadmap to Net Zero[4] lays out the various means by which the cement industry can achieve net-zero, including CCS (carbon capture and storage), fuel replacement and electrification, process efficiency, as well as decarbonisation of raw materials. Whilst the calcination process is fundamental to producing strong cement, certain natural and man-made materials (such as ash from coal fired power stations and slag from steel manufacture, both of which are no longer abundant resources) can substitute a proportion of the clinker and reduce the CO2 footprint of the cement. The availability of the raw materials will be a key factor in achieving this step of the decarbonisation process, and as such a variety of solutions are required.
The major focus of CO2 reduction in the cement industry is in naturally pozzolanic materials such as a group of raw materials referred to as calcined clays – naturally occurring clay deposits that are ‘pozzolanic’ (i.e., acts like cement) when heated in a kiln to around 700-800°C[5]. The term Pozzolanic derives from the Roman use of volcanic ashes from Pozzuoli near Naples from where the Romans derived the original cements. The science of cements was lost during the fall of the Roman Empire and was only rediscovered in the 1600s. Calcined clay pozzolans can be used to replace a proportion (up to 30%) of the cement clinker and are produced at a lower temperature than clinker for OPC. This provides a reduction of CO2 both in the process emissions of clinker calcination as well as the energy required for heating. This replacement alone is expected to achieve a reduction of 5-8% in total CO2 by 2050 and represents a 30% decrease in the carbon footprint of OPC.
Simple? Well, the science behind the process is somewhat more complex than that outlined above, and the availability and variation of suitable clay deposits may be a limiting factor. Even so, construction of Europe’s first full-scale clay calcination plant has now been completed in France for Ciment Vicat[6]. SLR have been supporting cement manufacturers in the exploration, testing, discovery and assessment of suitable materials. If you would like to find out more about the services we can provide please contact us.
References:
[1] https://www.linkedin.com/pulse/co2-emission-from-cement-industry-whats-best-estimate-claude-lorea/
[2] IEA Technology Roadmap – Low Carbon Transition in the Cement Industry. https://www.iea.org/reports/technology-roadmap-low-carbon-transition-in-the-cement-industry
[5] https://www.flsmidth.com/en-gb/discover/cement-2021/revealing-the-numbers-behind-calcined-clay
by Neil Vyas