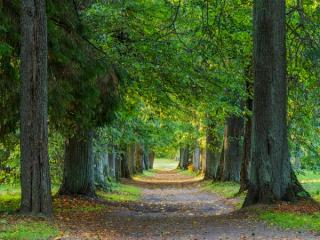
Human rights and the supply chain: Buying our way into trouble
- Post Date
- 24 July 2024
- Read Time
- 5 minutes
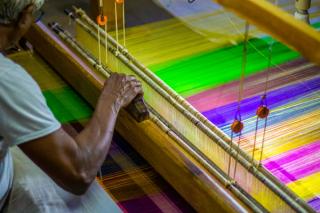
Think ‘human rights’ and most companies quickly think ‘supply chain’. Those long trade routes, snaking across the world to deliver the goods we love often end in low-income countries, with absent laws and weak enforcement. Workers’ and community rights are not always respected when we reach these lower tiers of our value chains.
Three broad categories of human rights and supply chain legislation
Trade sanction legislation, working to prevent or stop the movement of goods that are suspected to be made using forced labour e.g. the Uyghur Forced Labor Prevention Act in the US and the Forced Labour Regulation in the EU.
Due diligence legislation, requiring companies to understand the impacts their business has on the human rights of their own workforce and that of their value chain; and to demonstrate how they are mitigating those impacts (we call these ‘know and show’ laws), as in the EU Corporate Sustainability Due Diligence Act or Germany’s Act on Corporate Due Diligence Obligations in Supply Chains (LkSG).
Modern Slavery legislation, such as those in the UK, Canada and Australia, as well as California’s Transparency in Supply Chains Act.
In response, companies have worked hard to map and trace their producing factories and illuminate the risky hotspots. In the past couple of years, encouraged by a raft of new legislation (see above), they are now introducing due diligence and remediation processes. This logic goes: “somewhere down our supply chain are people whose rights are being abused, and as a good corporate citizen, we should find them and do what we can to help".
But what if we’re the problem?
These approaches are ‘camera out’ rather than ‘camera in’; looking for the human rights risks and impacts occurring at arm’s length in value chains. What if, instead, we asked if there were things we do in our companies that impact the human rights of the people in our supply chains?
And the first place to look inwards is to consider your purchasing decisions or practices.
‘Purchasing practices’ refer to the ways that businesses interact with their suppliers and manufacturers. The contracts, payment terms, risk sharing, scheduling and other commercial arrangements. Ideally these should provide a balance between a brand or retailer and their suppliers. There should be policies and processes in place that consider the needs of both the brand and the supplier to create a mutually beneficial partnership.
In practice these relationships are often deeply asymmetric, with the power held by the consumer-facing large business, leaving suppliers little choice but to accept the terms proposed. Buyers want it quicker, sooner, cheaper and better and suppliers have no option but to respond.
We have clear evidence that poor purchasing practices of this type directly affect workers – for example, long payment terms (even if contractually stated and agreed) can leave suppliers out of pocket, who may then have no choice but to hold back the salaries of the people working for them. Making a last-minute change to an order can leave suppliers scrambling to produce your product in the agreed lead-time, requiring their workforce to work excessive amounts of overtime, or relying on (potentially unauthorised) subcontracting to get the work done.
What do you know?
It’s not just the ethical sourcing teams that have responsibility for human rights. Suppliers are regularly visited by colleagues from Procurement, Quality, Merchandising and many other functions. Ensure supplier practice is Everyone’s Business and this app, developed by a consortium of retail companies, is a great way to informally collect and use the observations of colleagues.
Everyone's Business appThese issues are not exclusive to high-risk countries or sectors, and they cannot be found using a risk-based approach or through a risk tool. It requires a careful and sophisticated review of your whole buying approach – from design to delivery – looking at each stage for the downstream effect on suppliers.
But there’s a hugely positive reason to tackle it. When responsible purchasing practices are embedded, they build long-term relationships, improve quality and lower costs, in one case at least saving £7m a year in wasted samples when we stopped the blame ping-pong between a buying company and its Asian supplier.
They also go a long way to provide protection to all actors in the value chain, engendering trust and collaborative ways of working that help safeguard human rights.
Where to start?
Understand the current process for interacting with suppliers.This usually involves interrogating your critical path, assessing where decisions made an impact upon suppliers (e.g. forecasting, contracting, pricing, payment terms, etc.)
Consult with your suppliers. We have worked with many companies over the past few years, helping them understand the ways their purchasing decisions affect their suppliers. It is extremely rare for suppliers to interpret purchasing decisions in the same way that brands do. In fact, it is not unusual for them to be poles apart, with the brand thinking they consistently make positive purchasing decisions whilst the supplier experiences them very differently indeed.
It’s worth noting that supplier consultation can be difficult to do internally, as suppliers may be reluctant to be honest when asked for fear of business impacts – using an anonymous survey, a third-party, or leveraging an existing multi-stakeholder initiative are good ways of managing such concerns.
Tackle the issues raised through prioritisation. Where are your biggest impacts, and which of those are the most urgent?
As implementing human rights due diligence into business models becomes ever-more urgent, recognising the impacts of the way we do business will be key.
SLR is ready to support you in building better supply chain practices and relationships.
Let’s talkRecent posts
-
-
-
Navigating the evolving landscape of corporate sustainability and communications in the US
by Chynna Pickens
View post