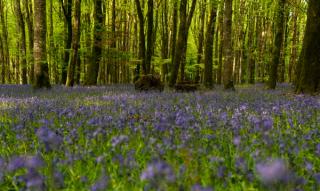
Four reasons automation in underground mining makes sense
- Post Date
- 08 January 2023
- Read Time
- 3 minutes
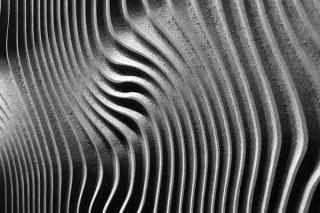
Automation in underground mining operations continues to be a ‘hot topic’ in our industry, but implementation has been slower than in other industrial applications such as automotive assembly plants. The reason for this lag relates to the nature of the underground mining environment. An underground mine is not a static environment, like a factory, leading to significant challenges in the implementation of automation in the various equipment. Despite this obstacle, mine automation has been progressing over the past ten to fifteen years and is now becoming more prevalent in mining operations globally.
Year over year, new technology in underground mining is turning automation into the norm – changing underground mining beyond recognition. In the future, it is imagined that underground mining operations may become fully automated without the requirement of humans working underground. In fact, back in 2015, the Northparkes mine did just this – it attained 100% automation for its block cave mine located in Australia. This was achieved by using driver-less loaders controlled from the surface to feed ore to an underground primary crushed where it is crushed, conveyed, and hoisted to the surface.
These advances in automation will provide huge benefits to mining companies and their employees by greatly improving safety and at the same time, increasing profitability through more efficient and productive operations.
So, if underground automation is on your agenda, what could it achieve for your operation?
- Safety: underground mining can pose significant safety risks to those that are operating in an underground environment. Automation can provide a safer work environment for operators. For instance, at a deep mine in Quebec, automation minimizes the workers' exposure to seismicity and high temperatures. In the case of production drilling, remote operation permits safely redrilling previously blasted holes eliminating operator exposure to potentially fatal explosions.
- Enhance productivity: automation can make operations faster and provides consistency and increased production. For instance, during times where productivity might drop, such as a shift change, mine blast or even a lunch break, automated equipment can continue to operate. When a mine is not producing, it is not making money, and therefore maximizing the utilization of the equipment leads to enhanced productively which in turn leads to increased profitability
- Enhance efficiency: many tasks underground, for instance rockbolting, scaling, drilling, etc., are very repetitive tasks. By automating these tasks, we can fully optimize the process, leading to a much more efficient operation, which again leads to increased profitability
- For corporations looking to enhance their Environmental, Social and Governance (ESG) mandates, mine automation provides opportunities to diversify the workforce by removing barriers to entry for certain underground mining jobs.
With deeper, more dangerous mining being carried out globally, the technology needed to create semi or fully autonomous vehicles is developing at a rapid pace. As the mining industry increasingly sees the value in automation, technology will enable the economic benefit of investing in new technologies to outweigh the risks, and companies will reap the benefits.
From a corporate perspective, automation supports ESG (environmental, social and governance) mandates and realizes opportunities for further workforce diversification, removing barriers to entry to some jobs and the industry as a whole.
To incorporate automation into a mining operation, the operation first needs a complete assessment; speaking with the team working underground, determining what is working now, why it is working and if anything could be improved. Any company considering automation is likely trying to find a solution to something or find a way to streamline operations to achieve specific business goals. It is important to understand these and determine how the automation, in whatever capacity, could achieve those goals.
Recent posts
-
-
-
Understanding sound flanking: Fire alarm speaker cable conduits in multi-family buildings
by Neil Vyas
View post